TAF’s most ambitious retrofit project to date is nearly complete. Last year, we announced a project with Toronto Community Housing at 575 Danforth Road. This 2-storey, 16-unit seniors’ apartment building is targeting 60% energy savings, 80% emissions reductions, and going for EnerPHit certification. The construction team, Joe Pace Contracting, together with the primary consulting team at WORKSHOP, have made some significant building upgrades over the past year. With the project nearing completion, I wanted to share more about the exciting progress we’ve made, without residents needing to leave their homes, thanks to innovative technologies.
Prefabricated panels expedite construction timelines
TAF has been coordinating with the on-site team every step of the way. In June, I saw the borehole excavation for the geothermal heat pump system. By September, the prefabricated wall panels made their way, from Simple Life Homes’ warehouse in Brighton to Scarborough, and they were installed them within 10 days. The prefabricated roof panels went up shortly after, in just two days. By the end of the year, Energy Recovery Ventilators (ERVs) and floor mounted fan coils had been installed in each unit. Shortly after, the condensing units for the heat pump system were installed, along with the new domestic hot water heat pump and tanks. Most recently, the construction team finished up the piping work and installed the building pumps. A pretty astonishing amount of work was completed in about a year!
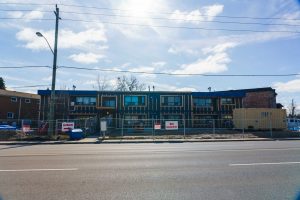
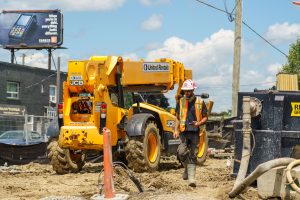
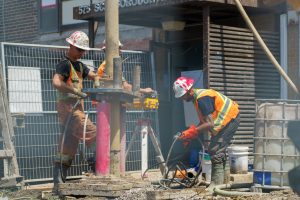
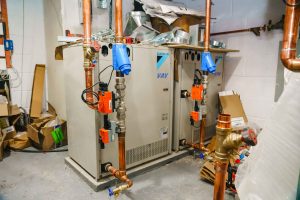
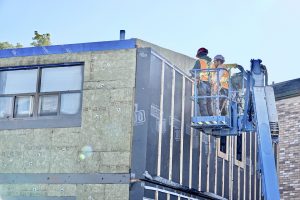
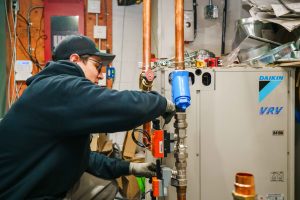
A key element of reducing on-site construction time while minimizing resident disruption was using prefabricated panels, which are well insulated, airtight wall systems that are manufactured off-site. Not only does this minimize weather-related delays, but it results in precise, high-quality construction in a controlled environment. The panels act as an insulated blanket for the building, reducing energy consumption and improving thermal comfort.
Prefabricated panels are an affordable, scalable technology that are becoming more essential as the need to rapidly mobilize retrofits increases, and they could play a key role in helping building owners to comply with upcoming regulations like building emissions performance standards. TAF is building a roster of pre-qualified suppliers, which will make it quick and easy for contractors across the GTHA to source local materials for their projects.
Tracking the co-benefits
When the project is complete, the benefits will extend beyond energy savings and lower emissions. Residents are especially excited about the ERVs, which will improve indoor air quality and humidity levels , and the cooling capabilities of the heat pumps. The building did not have fresh air supply nor central cooling prior to the retrofit. Our Retrofit Accelerator team will continue to monitor how the building’s Indoor Environmental Quality (IEQ) changes with the addition of central cooling, airtight wall systems, and ERVs. We’ve already gathered over a year of pre-retrofit data, monitoring parameters like temperature, humidity, carbon dioxide and particulate matter, and we expect to see an improvement in IEQ post-retrofit.
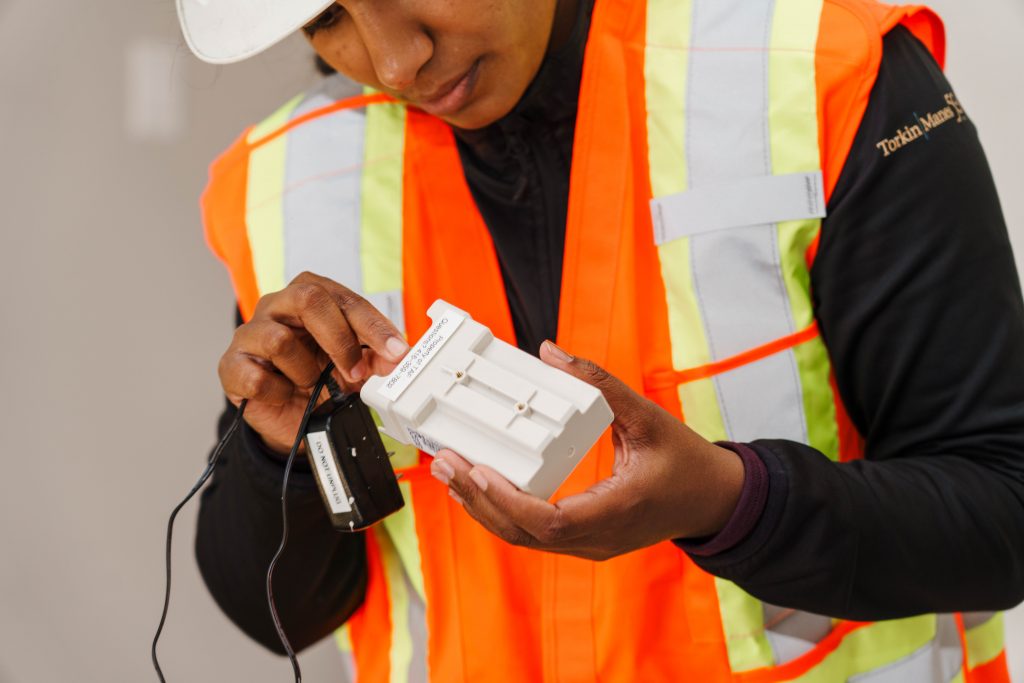
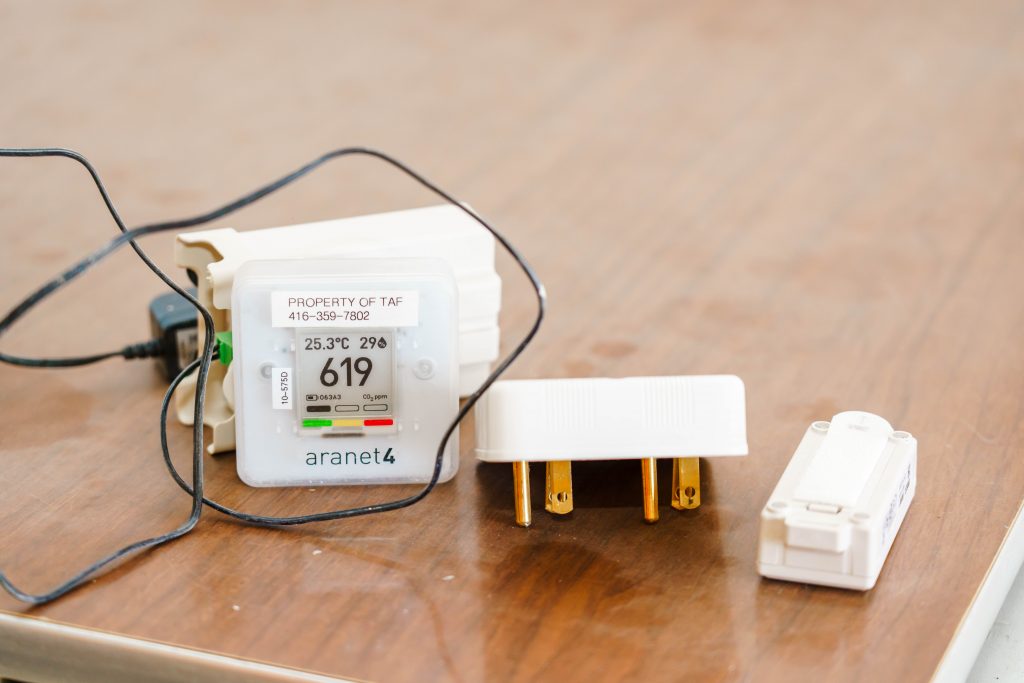
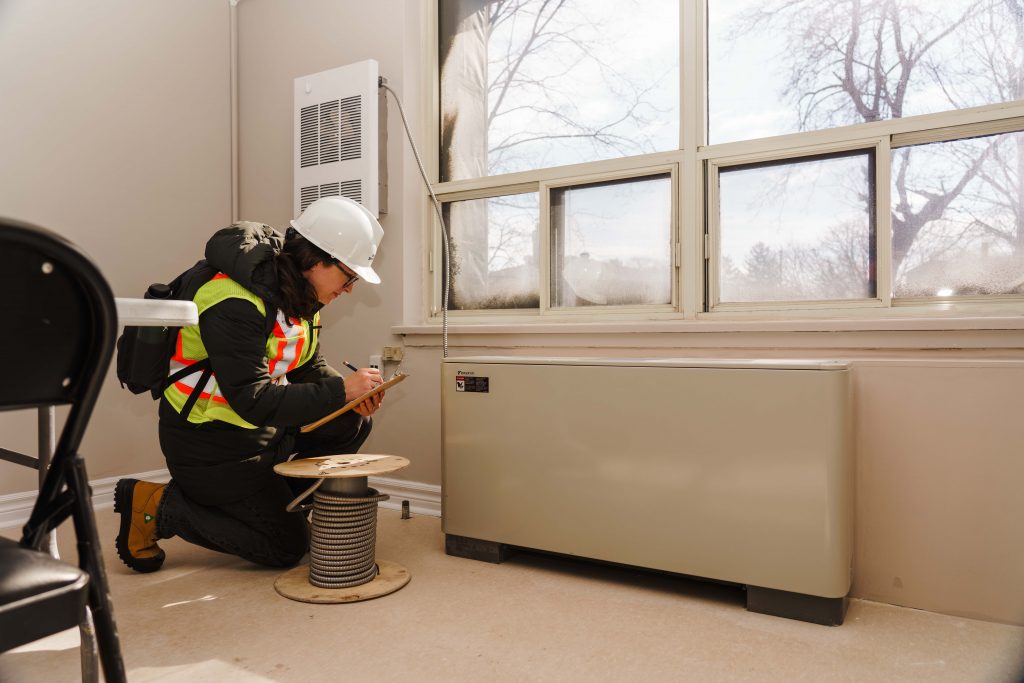
Next month, we’re going back to site to see the high-performance windows get installed and the final pieces of the envelope come together. With the right team and plan in place, deep energy retrofits can be completed efficiently with multiple co-benefits across the board. I’m excited to see how the last few months of work unfold and hear about the residents’ experience after it’s complete!
Hi Natasha,
I am the prime consultant who has been apart of the design and construction part of this project. Can you please update the article to mention WORKSHOP as the prime consultant involved?